Cranes are essential in construction, manufacturing, and logistics, engineered for heavy lifting and precise movement of large, often unwieldy materials. Their true efficiency and versatility shine when equipped with various attachments, enhancing their capabilities and ensuring safer, more effective material handling. This comprehensive guide explores the diverse world of crane attachments, examining their types, applications, and benefits.
What Are Crane Attachments?
Crane attachments are specialized devices affixed to a crane’s hook or jib, designed to handle different loads and perform various lifting tasks. These attachments are essential for tailoring the crane to specific operational needs. Common types include slings, spreader bars, lifting beams, and grab buckets, each addressing particular challenges in lifting and moving loads.
The Versatile Power of Slings
Slings are flexible lifting devices made from chains, wire ropes, or synthetic materials. They are versatile and used for lifting a wide range of materials. Chain slings are durable and ideal for heavy-duty applications, while synthetic slings are lightweight and gentle on delicate loads. Wire rope slings are often preferred in environments requiring high strength and resistance to abrasion.
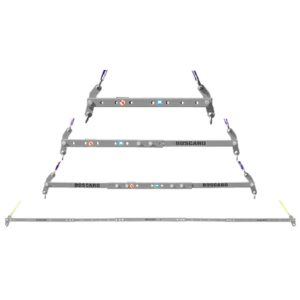
Spreader Bars
Spreader Bars: Balancing the Load
These are horizontal bars that help distribute the weight of a load evenly across multiple points. Spreader bars are particularly useful for lifting long, cumbersome loads that would otherwise be difficult to balance. They come in various designs, including fixed and adjustable models, to suit different lifting needs.
Lifting Beams
Similar to spreader bars, lifting beams are used to support loads at multiple points. They come in various configurations, including fixed and adjustable, and are essential for lifting wide, heavy, or awkwardly shaped objects. Lifting beams are often used with other lifting devices to ensure stability and safety during lifting operations.
Grab Buckets
These are mechanical devices that grasp materials like sand, gravel, or scrap metal. Grab buckets are typically used in industries such as mining and waste management where bulk materials need to be moved efficiently. They come in various designs, including clamshell and orange-peel models, each suited to different types of materials and lifting requirements.
Fork Attachments
Fork attachments transform cranes into giant forklifts. These are used to lift and transport pallets and other loads that can be handled by traditional forklifts, but where a forklift might not have the necessary reach or capacity. Fork attachments are particularly useful in warehouses and other storage facilities where large volumes of materials need to be moved quickly and efficiently.
Understanding the Role of Hoist Attachments
Hoist attachments are critical for lifting operations. These accessories connect to the hoist, enabling it to handle various types of loads with precision. Common hoist attachments include hooks, shackles, clamps, magnets, and vacuum lifters.
Hooks
Hooks are the most basic form of hoist attachment, used for general lifting purposes. They come in different sizes and shapes to accommodate various loads. Self-locking hooks are particularly useful for ensuring that the load does not accidentally slip off during lifting operations.
Shackles
Shackles are U-shaped pieces of metal secured with a pin or bolt across the opening. They are used to connect lifting slings, chains, and other attachments to the hoist. Shackles come in various sizes and designs, including anchor and chain shackles, each suited to specific lifting requirements.
Clamps
Clamps are used to lift loads with a secure grip. They are ideal for handling sheet metal, pipes, and other materials that might slip from traditional hooks or slings. Clamps come in different designs, including plate clamps and beam clamps, each designed for specific types of loads and lifting conditions.
Magnets
Magnets are specialized hoist attachments used for lifting ferrous materials. They are particularly useful in industries such as manufacturing and scrap metal processing, where handling steel plates, beams, and other iron-based materials is common. Magnets can be either permanent or electromagnets. Electromagnets provide the advantage of being able to control the magnetic force, allowing for easy attachment and release of materials. They ensure a firm grip on heavy, flat, or unevenly shaped loads, reducing the risk of slipping and enhancing safety.
Vacuum Lifters
Vacuum lifters are hoist attachments designed to lift non-porous materials using suction. They are ideal for handling items such as glass, metal sheets, and polished stone. Vacuum lifters create a vacuum seal on the material’s surface, allowing it to be lifted and moved without damaging the material. These lifters are particularly useful in environments where the material’s surface must remain unblemished, such as in glass manufacturing and installation, or in cleanroom settings. Vacuum lifters come in various configurations, including single-pad and multi-pad designs, to accommodate different sizes and weights of materials.
Crane Lifting Equipment Explained
Crane lifting equipment encompasses all the tools and attachments used to lift and move loads safely and efficiently. This includes both the crane itself and the various attachments designed to enhance its capabilities. The following are the key components:
The Crane
The crane is the primary lifting device, consisting of a boom, jib, or arm, and a hoist for lifting and lowering loads. Cranes come in various types, including mobile, tower, and overhead cranes, each suited for specific tasks. Mobile cranes are versatile and can be moved to different locations as needed, while tower cranes are fixed and used for high-rise construction projects.
Attachments
As discussed, attachments such as slings, spreader bars, and lifting beams are essential for adapting the crane to different lifting scenarios. These attachments help ensure that the crane can handle a wide range of materials and loads safely and efficiently.
Safety Devices
Safety devices, such as load indicators and limit switches, are critical for ensuring safe operation. These devices help prevent overloading and other dangerous conditions. Load indicators provide real-time information about the weight of the load, while limit switches prevent the crane from lifting beyond its maximum capacity.
Crane Under Hook Equipment
Crane under hook equipment includes all the devices and tools that attach directly to the crane’s hook. This material handling equipment is crucial for securing and lifting loads safely and efficiently. Proper use of under hook equipment enhances the versatility and capabilities of cranes, allowing them to handle a variety of loads with precision and stability. The main types of under hook equipment include:
Lifting Hooks
Lifting hooks are the most common under hook equipment, used for general lifting purposes. They come in various designs, including swivel hooks and self-locking hooks.
- Swivel Hooks: These hooks can rotate 360 degrees, allowing for easy rotation of the load. This feature is particularly useful in situations where the load needs to be precisely positioned or turned during lifting operations. Swivel hooks enhance maneuverability and help in aligning loads without needing to reposition the crane.
- Self-Locking Hooks: These hooks automatically lock when under load, ensuring that the load remains secure during lifting. This reduces the risk of the load slipping or becoming detached, enhancing safety. Self-locking hooks are ideal for operations where stability and security are paramount.
Shackles and Eyebolts
Shackles and eyebolts are essential for creating secure connections between the crane hook and the load. Shackles are U-shaped metal pieces secured with a pin or bolt across the opening. They are used to attach slings, chains, and other lifting devices to the crane hook. Shackles come in various sizes and designs, including anchor shackles and chain shackles. They are versatile and can handle a wide range of lifting tasks, making them a staple in crane operations.
Eyebolts are threaded bolts with a loop at one end, allowing for easy attachment to the load. They are often used for lifting heavy machinery and other equipment that can be threaded. Eyebolts provide a secure lifting point and are particularly useful in industrial and construction settings where heavy and irregularly shaped loads are common.
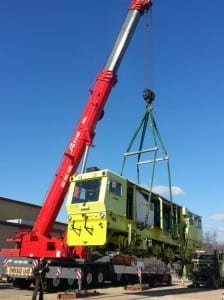
Active Crane Rental Hoists Train Car
Lifting Beams and Spreaders
Lifting beams and spreaders are devices designed to distribute the weight of a load across multiple points.
- Lifting Beams: Lifting beams are horizontal bars that support the load at multiple points. They are used to lift wide or heavy objects that would be difficult to balance with a single lifting point. Lifting beams come in various configurations, including fixed and adjustable designs, to suit different load requirements.
- Spreaders: Spreader bars function similarly to lifting beams but are typically used to distribute the weight of longer loads. They reduce the stress on the crane and the load by spreading it across multiple lifting points. This ensures a stable lift and minimizes the risk of damage to both the load and the crane.
Physics Behind Crane Operations
The operation of cranes is governed by basic principles of physics, particularly those related to leverage, balance, and load distribution. Understanding these principles is crucial for safe and efficient crane operation, ensuring that cranes can lift and move heavy loads with precision and minimal risk.
Leverage
Cranes use leverage to lift heavy loads with minimal force. The boom or jib acts as a lever, with the fulcrum being the point where the boom connects to the crane body. By adjusting the length and angle of the boom, operators can lift heavy loads with relatively little effort. The principle of leverage allows a smaller force applied at a greater distance from the fulcrum to lift a heavier load located closer to the fulcrum.
This mechanical advantage is what makes cranes capable of lifting extremely heavy objects that would otherwise be impossible to move manually. Additionally, the boom can be extended or retracted to change the lever arm, providing versatility in how loads are handled. This adaptability is particularly useful in varying job sites where different lifting requirements must be met.
Balance
Maintaining balance is essential for preventing tipping, a critical safety concern in crane operations. This is achieved by positioning the load correctly and using counterweights to offset the load’s weight. Counterweights are typically placed at the base of the crane to provide stability. They counteract the movement created by the load being lifted, preventing the crane from tipping over. The placement and amount of counterweight are carefully calculated based on the crane capacity and the boom’s length and angle.
Operators must also consider factors such as wind speed and ground conditions, which can affect balance. Proper training and awareness are crucial for operators to make real-time adjustments to maintain balance and ensure safe operation.
Load Distribution
Proper load distribution is critical for safe lifting. Using spreader bars and lifting beams helps ensure that the load’s weight is evenly distributed, reducing stress on the crane and the load itself. This is particularly important when lifting long or wide loads that might otherwise be difficult to balance.
Uneven weight distribution can cause the load to swing or shift unexpectedly, posing a risk to both the crane and the surrounding area. Spreader bars and lifting beams minimize the risk of damage to the load and the crane by distributing the weight evenly. They also improve control over the load during lifting and movement, enhancing safety and efficiency.
The Unique Capabilities of Jib Attachment Cranes
A jib attachment crane is a type of crane equipped with a jib, a horizontal or inclined arm used for lifting. The jib extends the crane’s reach, allowing it to lift loads at a greater distance from its base. This extended reach and flexibility make jib attachment cranes highly versatile and useful in various settings. Jib Cranes are used in the following sectors:
Construction
Jib cranes are commonly used in construction for lifting materials to different levels of a building. Their extended reach makes them ideal for this purpose, as they can efficiently transfer materials to higher floors without needing extensive repositioning. Jib cranes can be mounted on walls or floors, providing flexibility in placement and use. This adaptability allows construction teams to install jib cranes in optimal positions for maximum efficiency, whether they are used for hoisting bricks, concrete blocks, steel beams, or other construction materials.
Industrial Settings
In factories and warehouses, jib cranes are used for loading and unloading materials from trucks, moving goods within the facility, and positioning heavy machinery. They are often used in conjunction with other types of cranes and lifting equipment to provide comprehensive material handling solutions. The ability to mount jib cranes on walls or floors within industrial environments allows for efficient use of space and facilitates the smooth flow of materials throughout the facility. This is particularly beneficial in assembly lines, manufacturing processes, and storage spaces where precise positioning and easy access to materials are essential.
Marine Applications
Jib cranes are also used in marine settings for loading and unloading ships. Their flexibility and reach make them well-suited for handling cargo in these environments. They can be mounted on docks or on the deck of a ship, providing versatility in marine operations. In these applications, jib cranes are invaluable for transferring goods between ships and shore, as well as for managing cargo on board vessels. Their robust design and ability to operate in challenging marine conditions ensure that they can handle the demands of maritime logistics, whether it’s loading containers, handling bulk materials, or managing other types of cargo.
Improving Material Handling Equipment with UHA (Under Hook Accessories)
Under hook accessories (UHA) are crucial for enhancing industrial material handling operations. These accessories encompass a wide range of devices designed to securely attach loads to the crane’s hook, significantly boosting the crane’s versatility, safety, and efficiency.
Unmatched Versatility
UHA enables cranes to handle a diverse array of loads, from bulk material handling for construction to delicate machinery. This adaptability reduces the need for multiple lifting devices, allowing crane operators to quickly switch between different lifting tasks. Operators can tailor the crane to specific lifting requirements by employing various under hook accessories, thereby enhancing operational flexibility. This is particularly beneficial in environments where a wide range of materials must be handled, such as construction sites, factories, and warehouses.
Enhanced Safety
Using the correct UHA ensures that loads are secured properly, which is paramount for minimizing the risk of accidents. In industrial settings, where safety is a top priority, the proper securing of loads prevents them from shifting or falling during lifting operations. This reduces the risk of injury to workers and damage to materials.
Secure load handling is essential for maintaining a safe working environment, and the use of UHA plays a crucial role in achieving this. Accessories such as self-locking hooks, shackles, and clamps are specifically designed to provide a firm grip on various loads, ensuring stability throughout the lifting process. Discover more insights in our Guide to Crane Underhook Accessories for Safety & Efficiency.
Superior Efficiency
UHA streamline the lifting and rigging process, making it faster and more efficient. This efficiency can lead to significant time and cost savings in material handling process. UHA significantly enhances overall productivity by reducing the need for manual handling and ensuring the safe lifting and movement of loads.
For instance, the use of spreader bars and lifting beams allows for even weight distribution, which not only ensures stable lifting but also reduces the wear and tear on the crane and its components. Consequently, operations can proceed more smoothly, with fewer interruptions and a higher throughput of materials being moved.
Reduced Equipment Wear and Tear
Under hook accessories help distribute the load more evenly, minimizing the strain on the crane and its components. This balanced load distribution prevents overloading and reduces mechanical stress, extending the lifespan of the crane and its parts. By preventing undue wear and tear, UHA ensures that cranes operate more reliably and require less frequent maintenance, resulting in lower operational costs and increased uptime.
Improved Precision and Control
UHA enhances the precision and control of lifting operations. Specialized attachments like vacuum lifters and magnets allow for more accurate positioning and handling of materials, which is particularly important for delicate or high-value items. This improved control reduces the risk of damaging the load or the surrounding environment, ensuring that materials are handled with care and precision.
Greater Operational Flexibility
With a wide range of UHA available, cranes can be adapted to meet specific operational needs, from lifting oddly shaped loads to handling hazardous materials. This flexibility allows businesses to take on a broader range of projects and respond more quickly to changing job site requirements. UHA enables cranes to perform a variety of tasks without the need for additional specialized piece of equipment, making operations more adaptable and cost-effective.
Crane Accessories for Enhanced Performance
Crane accessories are additional tools and devices that enhance the performance of cranes. These accessories include items such as remote controls, load indicators, and safety devices.
Remote Controls
Remote controls allow operators to control the crane from a distance, improving safety and precision. This is particularly useful in hazardous environments where direct operation might be dangerous. Remote controls also allow for more precise positioning of the load, reducing the risk of damage to materials and equipment.
Load Indicators
Load indicators provide real-time information about the weight of the load being lifted. This helps operators avoid overloading the crane and ensures that the load is within safe limits. Load indicators are essential for maintaining safety and preventing damage to the crane and the load.
Safety Devices
Safety devices, such as limit switches and emergency stop buttons, are critical for preventing accidents. These devices automatically shut down the crane if dangerous conditions are detected, ensuring the safety of both the operator and the load. Limit switches prevent the crane from lifting beyond its maximum load capacity, while emergency stop buttons allow the operator to quickly halt lifting operations in case of an emergency.
Conclusion
Cranes are indispensable tools in various industries, and their true potential is unlocked through the use of specialized attachments and accessories. These tools not only enhance the crane’s capabilities but also improve safety and efficiency in material handling systems. Operators can make informed decisions that optimize their lifting operations by understanding the different types of crane attachments and their applications. Whether it’s using slings for versatile lifting, spreader bars for balanced loads, or remote controls for precise operation, choose the right accessories to make all the difference in achieving safe and efficient material handling.