Winter Safety Essentials: How Anemometers Protect Your Job Site in Harsh Conditions
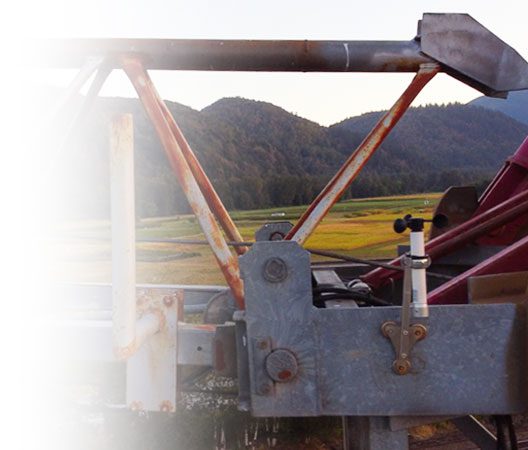
Protect Your Job Site in Harsh Conditions Winter weather can be unforgiving on construction sites, introducing unique challenges that compromise safety and efficiency. Among the most significant risks is high wind, which, combined with freezing temperatures, ice, and snow, poses dangers to workers, equipment, and operations. To ensure safety during harsh winter conditions, Bigfoot Crane […]
Safety and Efficiency in Elevated Work with a Crane Man Basket
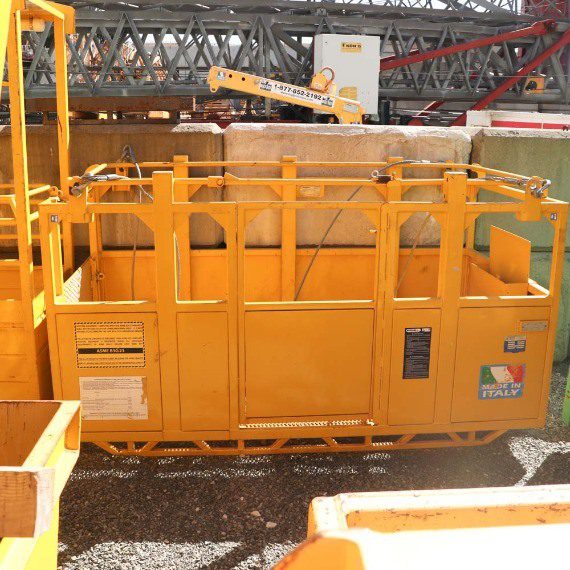
Crane man baskets are essential in lifting personnel to high, elevated places for work. They allow workers easier access to higher or hard-to-reach places enhancing safety and productivity in industries such as construction, and maintenance, among others. At Bigfoot Crane Company, we provide different types of crane man basket for sale and rental that are […]
Optimizing Crane Performance with Accessories and Attachments
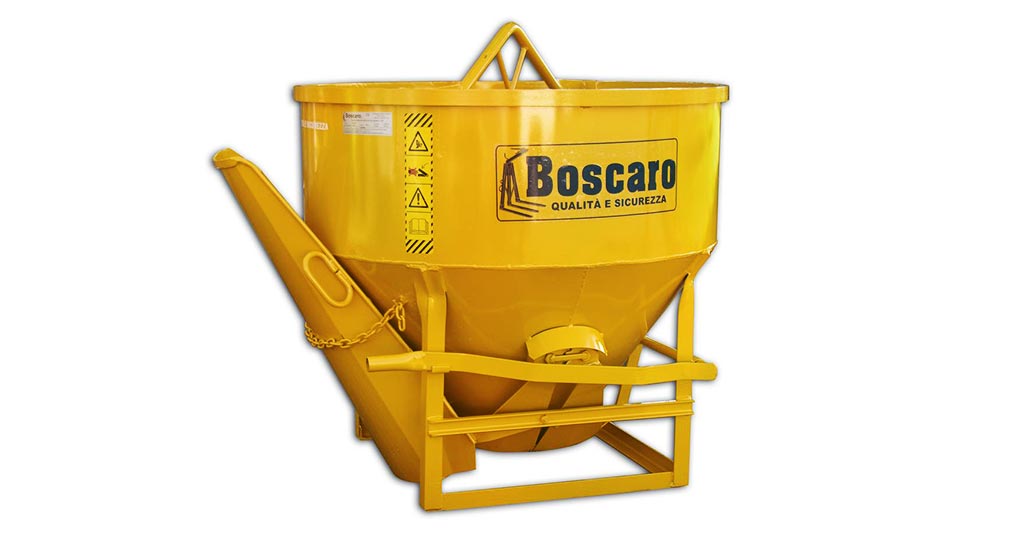
Crane attachments and accessories play a vital role in enhancing the functionality, safety and efficiency of cranes on various worksites. These add-ons extend the crane’s capabilities, allowing it to handle diverse tasks with improved versatility and precision. With the right combination of attachments, such as man baskets and concrete buckets, and essential accessories like lifting […]
Simplifying Concrete Placement with Reliable Concrete Buckets
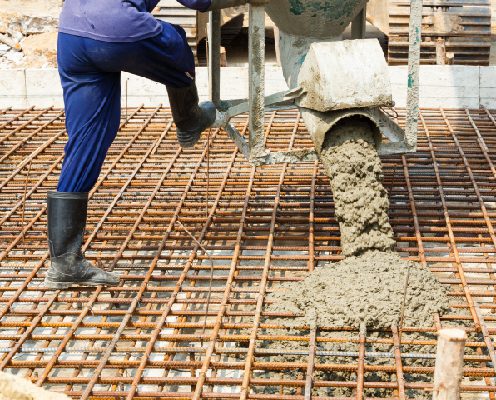
Concrete construction projects demand precision, efficiency, and reliability and concrete buckets play a pivotal role in achieving these goals by facilitating the placement of concrete in various construction scenarios. This article explores the significance of concrete buckets, the types, applications, benefits, and associated costs. Whether you are a seasoned professional or new to the field, […]
The Ultimate Guide to Protecting Your Construction Site This Winter
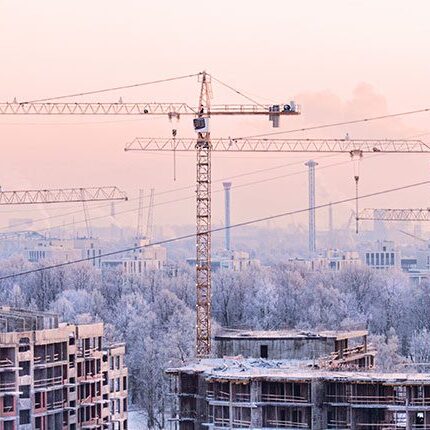
Winter weather poses unique challenges for construction sites, from freezing temperatures and high winds to snow and ice accumulation. To maintain safety and productivity, it’s essential to prepare your site for these harsh conditions. This guide outlines practical steps to protect your construction site during winter. Step 1: Prioritize Wind Monitoring with Anemometers Wind is […]
Mastering the Craft: Elevate Your Career with Level 1 Rigging Certification
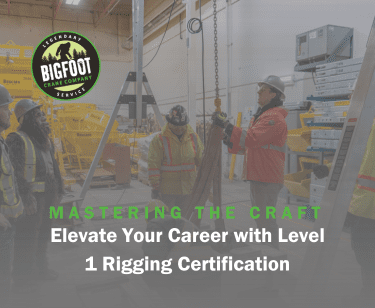
Gain essential skills with Bigfoot Crane Academy’s Level 1 Rigging Certification, blending classroom theory with practical training for a safe, skilled career in rigging.